Proceedings of 5th International Conference on Advanced Manufacturing Engineering and Technologies NEWTECH 2017 1st edition by Vidosav Majstorovic – Ebook PDF Instant Download/Delivery: 9783319564302, 3319564307
Full download Proceedings of 5th International Conference on Advanced Manufacturing Engineering and Technologies NEWTECH 2017 1st edition after payment
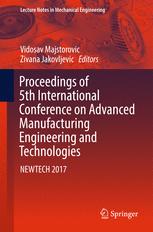
Product details:
• ISBN 10:3319564307
• ISBN 13:9783319564302
• Author:Vidosav Majstorovic
Proceedings of 5th International Conference on Advanced Manufacturing Engineering and Technologies
NEWTECH 2017
This book presents the proceedings from the 5th NEWTECH conference (Belgrade, Serbia, 5–9 June 2017), the latest in a series of high-level conferences that bring together experts from academia and industry in order to exchange knowledge, ideas, experiences, research results, and information in the field of manufacturing. The range of topics addressed is wide, including, for example, machine tool research and in-machine measurements, progress in CAD/CAM technologies, rapid prototyping and reverse engineering, nanomanufacturing, advanced material processing, functional and protective surfaces, and cyber-physical and reconfigurable manufacturing systems. The book will benefit readers by providing updates on key issues and recent progress in manufacturing engineering and technologies and will aid the transfer of valuable knowledge to the next generation of academics and practitioners. It will appeal to all who work or conduct research in this rapidly evolving field.
Proceedings of 5th International Conference on Advanced Manufacturing Engineering and Technologies NEWTECH 2017 1st Table of contents:
1 An Integration of Bio-inspired Algorithms and Fuzzy Logic for Tool Wear Estimation in Hard Turning
Abstract
1 Introduction
2 Experimental Design and Set-Up
3 Development of Fuzzy Expert Systems
3.1 GA Based Fuzzy Expert System
3.2 PSO Based Fuzzy Expert System
4 Results and Discussion
5 Conclusions
References
2 Hob Mill Profiling Method for Generation of Timing Belt Pulley
Abstract
1 Introduction
2 The Profile to Be Generated. Reference Systems. Generating Rack-Gear
3 Primary Peripheral Surface of Hob Mill
3.1 Kinematics of the Generating Process
3.2 Specific Enwrapping Condition
4 Numerical Application
5 Conclusions
Acknowledgements
References
3 Cyber Physical Production Systems—An IEC 61499 Perspective
Abstract
1 Introduction
2 RAMI4.0 Hierarchy Levels and Layers—A Brief Overview
3 Modeling of Distributed Control Systems Using IEC 61499
4 Case Study
5 Conclusion
Acknowledgements
References
4 Virtual Model in Monitoring and Optimization of a Selective Waste Collection Integrated System
Abstract
1 Introduction
2 Methodology
3 Virtual Model of the Selective Waste Collection System
4 System’s Diagnosis
5 System’s Optimization
6 Conclusion
Acknowledgements
References
5 An Advanced CAI Model for Inspection Planning on CMM
Abstract
1 Introduction
2 CAI Model
2.1 Mathematical Model
2.2 Inspection Features and Parameters
2.3 Sampling Strategy—Distribution Measurement Points
2.4 Collision Free-Generation and Probe Accessibility Analysis
2.5 Simulation and Optimization of the Measuring Path
3 Experiment
4 Conclusion
References
6 Flexible Control System Used in the Nano-technological Production Flow
Abstract
1 Introduction and Research Problems
2 Experimental Model
3 Results and Comments
4 Optoelectronic Control (Microscope with CCD Camera)
5 Conclusion and Future Research
References
7 Hydro-multipoint Forming, a Challenge in Sheet Metal Forming
Abstract
1 Introduction
2 Definition of Hydro-multipoint Forming
3 FEM Simulations of Hydro-multipoint Forming
3.1 Materials
3.2 Numerical Simulation
3.3 Results of Numerical Analysis
4 Experimental Work
5 Conclusions
References
8 Study on Hard Turning Process Versus Grinding in Manufacturing Some Bearing Inner Rings
Abstract
1 Introduction
2 Problem Definition
3 Experimental Methodology
3.1 Process Flow Description
3.2 Materials
3.3 Testing Procedure
4 Results and Discussions
4.1 Hard Turning Process
4.1.1 Cutting Speed Influence on Process Time
4.1.2 Feed Rate Influence on Process Time
4.1.3 Depth of Cut Influence on Process Time
4.1.4 Roughness and Surface Profile
4.2 Grinding Process
4.2.1 Roughness and Surface Profile
4.2.2 Roundness
5 Conclusions
Acknowledgements
References
9 On the Advanced Milling Technology of Thin-Walled Parts for Aerospace Industry
Abstract
1 Introduction
2 State of the Art
2.1 Study of the Material 7475-T7351
2.2 Theory of the Force Loading at Shoulder Milling
2.3 Surface Integrity of Machined Surface
2.4 Effect of Machining on the Surface Topography and Fatigue
3 Experimental
3.1 Tool Micro-geometry
3.2 Force Generation When Shoulder Milling
3.3 Measurement of the Surface Topography When Shoulder Milling
4 Results and Discussion
4.1 Tool Analyses
4.2 Cutting Conditions and Forces
4.2.1 Cutting Speeds and Forces
Feeds and Force
4.3 Cutting Conditions and Surface Topography
4.3.1 Surface Bearing Ratio, the Abbott-Firestone Curve
4.3.2 Feed and the Surface Bearing Ratio
4.3.3 Cutting Speed and the Surface Bearing Ratio
5 Conclusions
Acknowledgements
References
10 Reducing of Scuffing Phenomenon at HCR Spur Gearing
Abstract
1 Introduction
2 HCR Gearing and Possibilities of Optimization of Geometrical Parameters
2.1 Interference During the Production
2.2 Interference During the Production
2.3 Minimum Thickness of the Tooth Head Circle
2.4 Optimization of HCR Geometry
3 Scuffing as the Most Important Damage of HCR Tooth Flanks
4 Calculating the Tooth Scuffing Resistance According to the Criterion of Integral Temperature
4.1 General Principles of the Integral Temperature Criterion in HCR Involute Gearing
4.2 Calculating Medium Temperature of the Tooth Surface ϑBlm for HCR Involute Gearing
5 Joined Optimization of Geometrical and Scuffing Parameters of HCR Gearing
6 Conclusions
References
11 Parametric Design of an Electric Driven Reduction Gear for Anchor and Mooring Winches
Abstract
1 Introduction
2 Graphical Modelling of Reduction Gear Elements
3 Algorithm for Reduction Gear Calculation
3.1 Choosing the Electric Motor
3.2 Choosing the Gear Ratio
3.3 Choosing the Teeth Number of Toothed Wheels
3.4 The Toothed Wheel Calculation of Resistance
4 Methodology for Parameters Configuration
5 Conclusions
Acknowledgements
References
12 Experimental Determination of Brittle Fracturing Appearance During Static Indentation of Material
Abstract
1 Introduction
2 Static Indentation
3 Experimental Setup
4 Results and Discussion
5 Conclusion
References
13 Dynamic Optimization of the Cam-Lever Mechanism for Thermoforming Machine Tool Driving
Abstract
1 Introduction
2 Thermoforming Process
3 Working Mechanism
4 Dynamic Optimization
4.1 Optimization Problem
4.2 Results
5 Conclusions
References
14 Cyber-Physical Manufacturing Systems (CPMS)
Abstract
1 Introduction
2 The Development of Cyber-Physical Manufacturing Concept
3 Towards Real CPMS Application
4 Industry 4.0 Model
5 Conclusion
Acknowledgements
References
15 Graphical Method in CATIA for Side Mill Tool Profiling Using the Generating Relative Trajectories
Abstract
1 Introduction
2 The Relative Generating Trajectories Method
3 Applications
3.1 Side Mill for the Helical Flute of a Helical Drill
4 Graphical Method Developed in CATIA
5 Conclusions
Acknowledgements
References
16 Mechanistic Approach for the Evaluation of Machine Tools Quasi-Static Capability
Abstract
1 Introduction
2 State of the Art
2.1 Various Sources of Error in Machine Tools
2.2 Errors Under Quasi-Static Condition
2.3 Parameters of Machine Tool Geometric Errors
2.3.1 Component Errors
2.3.2 Location Errors
2.4 Stiffness of Machine Tools
3 The Proposed Methodology
3.1 Case Study
3.2 Direct Measurement Model
3.2.1 Direct Measurement of Geometric Errors
3.2.2 Geometric Error Model Development
3.2.3 Measurement Data Integration to the Model
3.2.4 The Predicted Geometric Errors
3.3 The Indirect Measurement Model
3.3.1 The Loaded Double Ball Bar Measurement Process
3.3.2 Stiffness Prediction for Machine Tools
3.3.3 Static Stiffness Variation
4 Conclusions
Acknowledgements
References
17 Assessment of Assembly Process Complexity and Modularity in Mass Customized Manufacturing
Abstract
1 Introduction
2 Related Work
3 Proposed Approaches to Quantification of Product Complexity and Process Modularity
3.1 Assessment of Product Complexity
3.2 Assessment of Process Modularity
4 Application of the Proposed Approaches on a Case Study
5 Conclusions
References
18 A Holistic Approach for Developing and Commissioning Data Driven CPPS Functionality in Manufactur
Abstract
1 Motivation
2 Introductions to Cyber-Physical Production Systems
2.1 Cyber-Physical Systems
2.2 Cyber-Physical Production Systems
2.3 Methodology to Transform Production Systems into CPPS
3 Application Example Suspension Turret
3.1 Investigated Process
3.2 Creation of the Mathematical Model
3.3 Implementation into the Machine Control
4 Conclusion and Outlook
References
19 Some Aspects Influencing Production of Porous Structures with Complex Shapes of Cells
Abstract
1 Introduction
2 State of the Art
3 Regular Porous Structures Design
4 Experiments
5 Conclusions
Acknowledgements
References
20 Recovery of Metals from Solar Cells by Bioleaching
Abstract
1 Introduction
2 Materials and Methods
2.1 Determination of Metal Content of Solar Cells
2.2 Growth of Micro-organisms and Collection of Cell-Free Supernatant
2.3 Bioleaching of Solar Cells by Using Culture Supernatant
2.4 Effect of Physicochemical Parameters on Bioleaching of Metals from Solar Cells
2.5 Analytical Methods
3 Results and Discussion
3.1 Bioleaching of Metals from Solar Cells
3.2 Effect of Temperature
3.3 Effect of Shaking Speed
3.4 Effect of Pulp Density
4 Conclusion
References
21 Intelligent Wear Identification Based on Sensory Inline Information for a Stamping Process
Abstract
1 Introduction
2 Wear Mechanism for Shear Cutting Tools
3 Experimental Setup and Procedure
4 Characteristic Process Parameter for Wear Identification
5 Establishing Characteristic Parameters for the Wear Status of the Tool
6 Conclusion and Outlook
Acknowledgements
References
22 High-Precision Machining of Hard Steel Parts Using Special Abrasive Operations
Abstract
1 Introduction
2 Experimental Details
2.1 Characterization of Workpiece Material and Machining Conditions
2.2 Measurements of Surface Roughness Parameters
3 Experimental Results and Discussion
3.1 Characterization of Machined Surfaces
3.2 Characterization of Function Related Parameters
3.3 Characterization of Spatial and Hybrid Parameters
3.4 Surface Characterization Based on Motifs and Fractals
4 Conclusions
References
23 Process and Microstructure in Materials-Affected Manufacturing
Abstract
1 Introduction
2 Microstructure Evolution Modeling
2.1 Phase Transformation and Dynamic Recrystallization of Ti–6Al–4V
2.2 Dynamic Recrystallization of 4130 Steel
3 Microstructure Sensitive Flow Stress Model
4 Phase Transformation and Grain Size Prediction
5 The Force Prediction
6 Residual Stress Prediction
7 Conclusion
References
24 Structural FEM Analysis of Thermal Sprayed Coatings Under Conditions of Contact Pressure and High
Abstract
1 Introduction
2 FEM Structural Simulations Preparations
2.1 Geometry for Simulation
2.2 Loads and Temperature
2.3 Boundary Conditions
2.4 Meshing and Mathematical Model
2.5 Simulation Characteristics
2.6 Material Properties
2.7 Simulation Plan
3 Simulation Results
3.1 Contact Pressure
3.2 Thermal Stress
3.3 Complex State
3.4 Correlations
4 Conclusions
References
25 Intelligent Dual Curve-Driven Tool Path Optimization and Virtual CMM Inspection for Sculptured Su
Abstract
1 Introduction
2 Intelligent Tool Path Parameter Selection for Dual-Curve Driven Trajectories
2.1 Dual-Curve Driven Multi-axis Surface Tool Paths
3 Experimental Results
3.1 Fitness Function Formulation and Genetic Algorithm Parameters
3.1.1 Simulation Results
3.1.2 Virtual CMM Inspection Results
4 Conclusions
References
26 Advanced Manufacturing and Industrie 4.0 for SME
Abstract
1 Introduction
2 Characteristic of the International Situation
3 Industrie 4.0 Key Features and Aspects
References
27 Industrial Product Life Cycle Stages and Lifecycle Eco-design
Abstract
1 Introduction
1.1 Sustainable Consumption and Production
2 Eco-design
2.1 The Content of Eco-design Process
2.1.1 Product Improvements
2.1.2 Product Design
2.1.3 New Product Design
2.1.4 New Production System
2.1.5 Essentials for Adopting Eco-design Strategies
2.1.6 Eco-design Strategies According with Circular Economy Principles
3 Product Life Cycle Stages and Lifecycle Eco Design Strategies [2, 3]4 Conclusions
References
28 Study on the Machinability Characteristics of Inconel 718 Super Alloy During Micro-Milling
Abstract
1 Introduction
2 Experimental Setup
3 Results and Discussion
4 Conclusions
References
29 A Multi-parameter Experimental and Statistical Analysis of Surface Texture in Turning of a New Al
Abstract
1 Introduction
2 Surface Roughness Parameters
3 Experimental
4 Results and Discussion
4.1 Variation of Surface Roughness Parameters
4.2 Chip Formation and Tool Wear
4.3 Statistical Analysis and Regression
5 Conclusions
References
30 Influence of the Determination of FLC’s and FLSC’s and Their Application for Deep Drawing Pro
Abstract
1 Introduction
2 Material Modelling
3 Damage Modelling
3.1 Strain-Based Damage Models and Results
3.2 Stress-Based Damage Models and Results
4 Deep Drawing with Additional Force Transmission
5 FEA of Deep Drawing Process
6 Summary and Outlook
Acknowledgements
References
31 Biologically Inspired Optimization Algorithms for Flexible Process Planning
Abstract
1 Introduction
2 Flexibilities and Representation of the Process Planning Problem
3 Mathematical Modeling and Optimization Objectives
4 Biologically Inspired Optimization Algorithms
4.1 Genetic Algorithms
4.2 Simulated Annealing
4.3 Chaotic Particle Swarm Optimization Algorithm
4.4 Ant Lion Optimization Algorithm
5 Experimental Results
6 Conclusion
Acknowledgements
References
32 Modelling and Analysis of 3-Axis Reconfigurable Hybrid Kinematics Mechanism with Translatory Actu
Abstract
1 Introduction
2 Description of 3-Axis Hybrid Kinematics Mechanism
3 Geometric Model of Hybrid Mechanism MOMA3_HK and Solving the Kinematic Problem
3.1 The Solution of Inverse Kinematic Problem
3.2 The Solution of Direct Kinematic Problem
4 Workspace of Hybrid Mechanism MOMA3_HK
5 Jacobian Matrix and Singularity Analysis
6 Conclusion
References
33 Influence of Ultrasonic Assistance on Delamination During Machining of CFRP Composite
Abstract
1 Introduction
2 Machining Method
3 Description of the Experiment
4 Results of the Experiment
5 Conclusion
Acknowledgements
References
34 Microfluidic Chip Fabrication for Application in Low-Cost DIY MicroPIV
Abstract
1 Introduction
2 Fabrication of a Chip
3 MicroPIV System for Microfluidic Purposes
4 Properties, Possible Modifications and Potential Applications of the Microfluidic System
5 Conclusion
Acknowledgements
References
35 R&D in a Fab Lab: Examples of Paste Extrusion Method
Abstract
1 Introduction
1.1 3D Printer Modifications
2 Paste Extrusion with Clay
3 Paste Extrusion with Chocolate
4 Paste Extrusion with Modified Hydroxy-Apatite
5 Discussion
Acknowledgements
References
36 Manufacturing Technology of Aircraft and Wind Turbine Blades Models, Plugs and Moulds
Abstract
1 Introduction
2 Current Concepts and a Connection to Fab Lab
3 Process Description
4 Possible Applications and Produced Parts
4.1 Amphibian Aircraft Model
4.2 Composite Blade Master Plug
4.3 Wind Turbine Production Mould
5 Conclusions
Acknowledgements
References
People also search for Proceedings of 5th International Conference on Advanced Manufacturing Engineering and Technologies NEWTECH 2017 1st:
proceedings of 5th international conference
proceedings of the 53rd hawaii international conference on system sciences
5th international conference
proceedings of the 52nd hawaii international conference on system sciences
proceedings of the national conference on undergraduate research